Relocation for Environmental Labs: Planning and Executing
Ted Palashis | October 22, 2021
Environmental labs do a wide array of studies, discovering, collecting, and analyzing data that provides a variety of applications. From the natural components of the Earth, like soil, water, and air, to more complex variables like waste characterization, contaminants, and other eco-forensics, the research, planning, and oversight in this sector is as complicated as it is important in achieving new environmental discoveries and solutions. When an environmental laboratory needs to update, upgrade, or expand, its relocation is an equally important task with critical components that need to be accounted for, addressed, and executed.
There are four key pillars in a successful laboratory relocation. Communication management, understanding laboratory operations, comprehensive relocation planning, and move management execution are all critical in safely, effectively, and efficiently relocating a laboratory. Let’s take a closer at creating a relocation plan and executing the relocation itself.
Environmental Laboratory Relocation Planning
The transition of your laboratory and its assets needs to be led by a carefully calculated strategy based on experience and expertise that mitigates potential risks. Complications and other factors can quickly derail the relocation process causing budget overruns, schedule delays, asset damage, and compromise critical data. A thorough site assessment and a realistic, detailed schedule created and performed by a team of dedicated project managers and subject matter experts will ensure a compliant move with minimal downtime.
Environmental Laboratory Relocation Execution
Once a comprehensive plan is in place, it is time for the relocation itself. The execution of this process begins with the decommission and deinstallation of the lab’s instrumentation. These assets, along with other supplies, will be properly handled and packed for transportation. Transportation isn’t limited to the back of a truck. This process from point A to point B involves every step taken when in between where these instruments were and will be. Once at the new site, the assets will be unpacked and reinstalled. The final stage of the relocation will involve the qualification of all instrumentation, ensuring that it is optimized and ready to perform in its new location.
Relocation planning and execution is a full-time job, which is why the experienced, expert engineers and project managers at Overbrook handle it for you. With proven strategies and experience, downtime, cost, and risk can all be mitigated by outsourcing your next relocation.
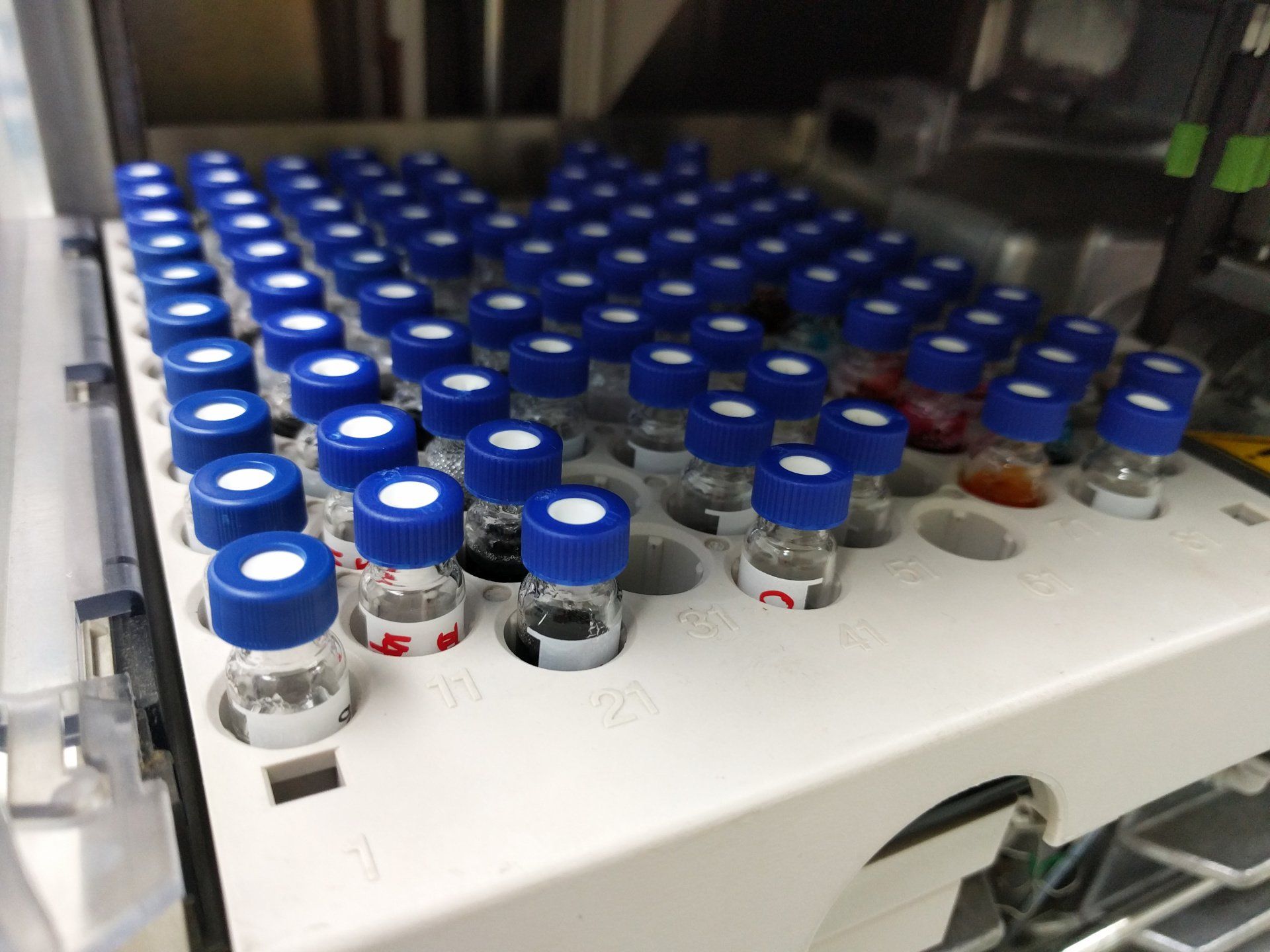
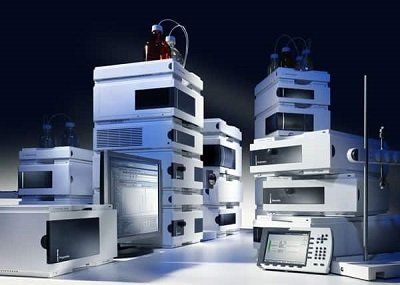